Sprutbetong används först och främst för att förstärka tunnlarna i gruvan. Betongen appliceras med hjälp av tryckluft på väggar och tak med en tjocklek av 70 eller 100 millimeter. Betongfabrikerna i Malmberget och Kiruna ser till att leverera en årlig volym på sammanlagt 70 000 – 80 000 kubikmeter för ändamålet. Sammanlagt ”säkras” 20 000 – 30 000 meter tunnel årligen.
– Betongen är fiberarmerad för att bli ännu kraftigare och starkare, säger Benjamin Krutrök.
– Allt arbete från tillverkning till sprutning utförs i egen regi, vilket gör att vi har hundraprocentig koll på hela flödet, säger Sofia Utsi, avdelningschef vid LKAB Berg & Betong.
– Jag har rest mycket i branschen och sett att det på sina håll kan uppstå problem av olika slag när personalen för sprutningen respektive betongproduktionen, kommer från olika företag. Eftersom vi tar ansvar för hela processen så kan vi till exempel göra kvalitetsändringar eller utveckla betongrecept och se hur det påverkar helheten. På så sätt arbetar vi hållbart och med hög kvalitet, samtidigt som vi minskar mängden deponerad betong, fortsätter Benjamin Krutrök.
En annan produkt är vältbetong som går till vägbeläggning i gruvan, framför allt i Malmberget. LKAB Berg & Betong levererar dessutom byggbetong till samhällsomvandlingen i hela Malmfälten.
Vi har hundraprocentig koll på hela flödet
Sofia utsi, avdelningschef LKAB Berg & Betong
Fyllning av trasiga schakt
Ett annat område är renovering av trasiga schakt i Kiruna. De har ofta en tendens att bli större och större när det rasar ned berg från sidorna, som till exempel kan leda till att schaktet täpps igen. Därför fylls schaktet igen med betong, betongen härdar och sedan borrar man upp ett nytt hål genom det gamla.
På det området har det tidigare krävts stora mängder cement till betongen, men för några år sedan började cementen som bindemedel i betongen att ersättas till 50 procent av GGBS*, en restprodukt från ståltillverkningen.
- På detta sätt har vi nästan halverat klimatavtrycket, fortsätter Benjamin Krutrök.
Genom tillsättning av GGBS sänktes värmeutvecklingen jämfört med när man hade enbart cement som bindemedel. På så sätt blir det också bättre kvalité på betongen. För när arbeten med trasiga schakt sker krävs cirka 20 000 – 30 000 kubikmeter betong i en gjutning som tar cirka två månader.
Nu pågår försök med att helt ersätta cementen med GGBS och en restkalk från rökgasrening som annars deponeras. Tillsammans med återvunnet gråberg, som används som ballast, skapas en betong med återvunna delmaterial och låga koldioxidutsläpp. 2006 var företaget ett av de första i Sverige som fasade ut naturgrus mot krossad ballast som tillvaratas från järnmalmsbrytningen och på så sätt sparas naturresurser.
Cement och GGBS kommer med båt till hamnarna i Skellefteå och Luleå, därifrån blir det sedan järnväg till Kiruna respektive Malmberget.
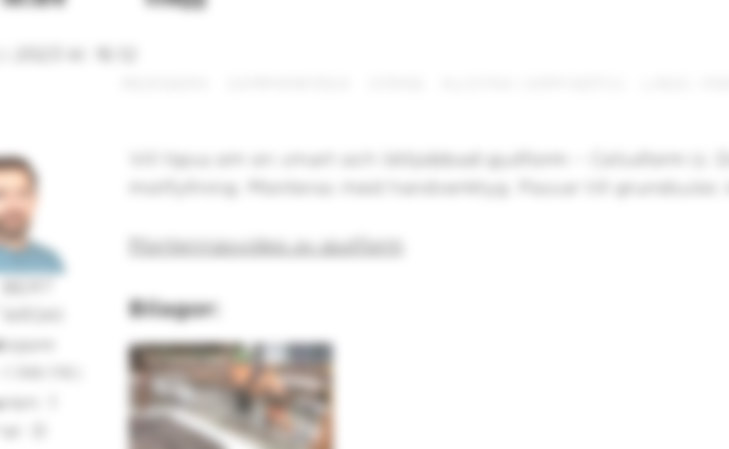
Vad tycker du?
Delta i diskussionerna på vårt Forum, en exklusiv mötesplats för dig i byggbranschen.
Anslut dig till en gemenskap av passionerade byggare!
Miljöarbete - ett mantra
Att minska koldioxidutsläppet är något som ständigt återkommer på den dagliga agendan. Oljepannorna har tidigare drivits av fossilt bränsle för att kunna ”värma upp” ballast som lagras utomhus, något som i synnerhet behövs vintertid med temperaturer ned till cirka 30 minusgrader. Uppvärmning görs till ett antal plusgrader så produkten ska kunna hanteras vidare. Det fossila bränslet har nu ersatts av biolja HVO 100. Miljövinst: 70 procent lägre koldioxidutsläpp jämfört med tidigare.
De tidigare fossildrivna bilarna inom betongtillverkningen i Kiruna har bytts ut till eldrivna fordon.
Det gamla talesättet ”Många bäckar små gör en stor å” är något som verkligen känns aktuellt för LKAB Berg & Betong. Även om bäckarna i detta fall är i kolossalformat.
*Fotnot: GGBS, ground granulated blast furnace slag. Fritt översatt: mald granulerad masugnsslagg som är en restprodukt från råjärnstillverkning.
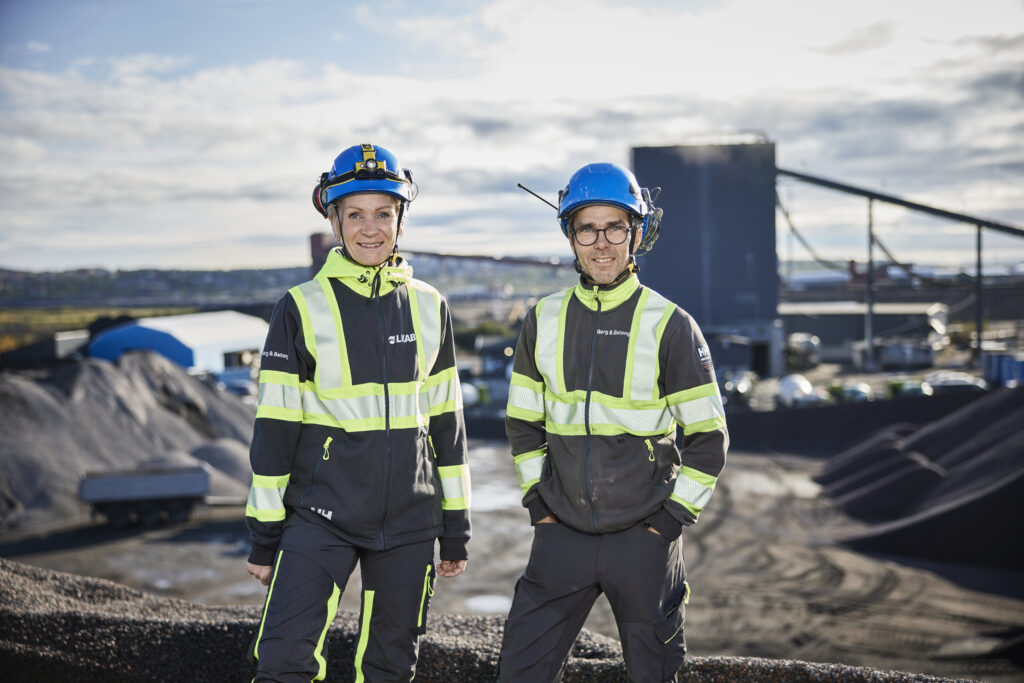
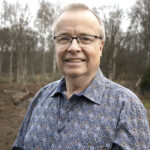